Aluminum Casting Mastery: Methods and Tools for Exceptional Outcomes
Understanding the art of light weight aluminum spreading requires a fragile equilibrium of precision, method, and the application of specialized tools. As we check out the intricate strategies and devices entailed in aluminum spreading mastery, one can not overlook the importance of innovative pouring and cooling down methods that can raise the last outcome.
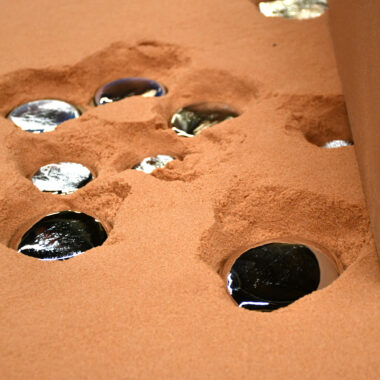
Importance of Correct Melting Strategies
Making use of exact temperature level control during the melting procedure is critical in making certain the quality and honesty of aluminum spreadings. The melting of aluminum is a crucial action in the spreading process, as it directly influences the last buildings of the casted parts. Appropriate melting techniques are necessary to accomplish the preferred metallurgical structure, mechanical properties, and surface area finish of the light weight aluminum parts.
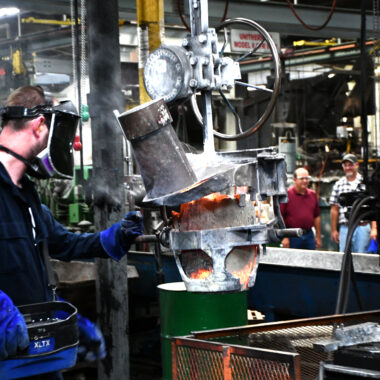
In addition, surveillance and readjusting the melt temperature level throughout the process aid prevent overheating, which can cause grain development and affect the overall quality of the light weight aluminum casting. Complying with precise melting strategies not just boosts the top quality of the last item but additionally boosts the performance and cost-effectiveness of the casting process.
Crucial Mold Preparation Tips
Proper prep work of molds is a fundamental element in the light weight aluminum spreading process, guaranteeing the successful replication of elaborate information and dimensions in the final casted components. Prior to putting the molten light weight aluminum, the mold tooth cavity have to be meticulously cleansed and dried to prevent flaws in the casting.
Furthermore, correct gating and risering style are vital in mold and mildew prep work to ensure audio spreadings with marginal problems like porosity and contraction. Eviction system helps with the circulation of molten metal right into the mold and mildew cavity, while risers aid avoid contraction by providing extra molten steel as the casting strengthens. Cautious factor to consider of these aspects during mold and mildew preparation significantly contributes to the top quality and stability of the last light weight aluminum cast components.
Advanced Pouring and Cooling Techniques
Applying advanced putting and cooling methods is crucial in enhancing the light weight aluminum casting process for enhanced efficiency and high quality end results. Utilizing strategies such as vacuum casting can considerably lower porosity in the end product, causing enhanced mechanical homes. By leaving the air from the mold and mildew tooth cavity prior to pouring, the risk of gas entrapment is minimized, resulting in this content a denser and even more structurally sound casting.
Moreover, using regulated cooling approaches, such as water quenching or air cooling, can influence the product's microstructure and mechanical attributes (about aluminum casting). Rapid cooling can aid attain finer grain frameworks and boosted mechanical homes, making the cast aluminum preferable for applications calling for high toughness and toughness
Furthermore, applying directional solidification techniques, where the casting strengthens considerably from one end to an additional, can assist alleviate inner issues and boost general part stability. By meticulously handling the temperature differentials throughout solidification, the development of shrinkage porosity and hot splits can be reduced, resulting in better spreadings with boosted mechanical performance.
Vital Tools for Light Weight Aluminum Casting
Enhancing the effectiveness and top quality results of light weight aluminum spreading procedures counts heavily on the utilization of details devices made to maximize various facets of the spreading operation. One important device for light weight aluminum spreading is the crucible. Crucibles are containers made from products like clay-graphite or silicon carbide that withstand the heats required for melting aluminum. Crucibles are available in different dimensions to fit various spreading quantities and are crucial for melting and putting the liquified light weight aluminum.
Another vital tool is the mold. Molds can be made from materials like sand, plaster, or steel and are made use of to shape the liquified light weight aluminum into the preferred kind. about aluminum casting. Proper mold and mildew design and materials are visit homepage important for accomplishing exact casting measurements and surface area coatings
Along with mold and mildews and crucibles, a heater is a basic device for light weight aluminum spreading. Heating systems warm the steel to its melting factor, ensuring it is in a state ready for casting. Essential for preserving constant temperatures and ensuring the aluminum continues to be liquified, heating systems are available in different types, such as electrical, gas, or induction heaters, each with its advantages for certain casting demands.
Ending Up Touches and High Quality Checks
Upon finishing the spreading process, careful attention to completing touches and strenuous high quality checks is critical to ensure the stability and accuracy of the light weight aluminum elements - about aluminum casting. Ending up touches involve the elimination of any excess material, such as flash, gating systems, or rough edges, to attain the wanted last form and surface area high quality. This step often includes processes like grinding, sanding, or fired blasting to refine the appearance and texture of the cast components
Quality checks are then carried out to validate that the parts satisfy the specified requirements and criteria. These checks might entail dimensional assessments making use of accuracy devices like calipers or coordinate measuring devices to guarantee precision. In addition, non-destructive testing techniques such as ultrasonic screening or X-ray examination can be employed to identify any type of interior problems that might jeopardize the architectural stability of the parts.
Verdict
Finally, grasping aluminum spreading techniques and utilizing the right tools is important for achieving outstanding results. Correct melting techniques, mold preparation, putting and cooling down methods, in addition to completing touches and quality checks are crucial action in the casting procedure. By following these actions carefully and using the appropriate devices, one can ensure a effective and high-quality aluminum casting production.
As we check out the complex strategies and tools involved in light weight aluminum spreading proficiency, one can not forget the relevance of advanced putting and cooling down techniques that can elevate the final result.Appropriate prep work of mold and mildews is a fundamental facet in the aluminum casting process, ensuring the successful duplication of intricate information and measurements in the last casted components. browse around these guys Prior to pouring the molten aluminum, the mold and mildew cavity have to be carefully cleaned up and dried to protect against problems in the casting.Enhancing the effectiveness and high quality outcomes of light weight aluminum casting procedures relies heavily on the application of particular tools made to optimize various aspects of the casting procedure.In enhancement to mold and mildews and crucibles, a furnace is a fundamental tool for light weight aluminum casting.